What is Hydraulic Pressure and Why is it Important?
Hydraulic pressure offers a straightforward yet incredibly effective way to generate substantial force in a limited area. It harnesses the power of hydraulic fluid pressure to create this force. From the early days of low-pressure, hefty hydraulic lifting jacks to today’s cutting-edge high-pressure hydraulic systems, hydraulic power has consistently served as a highly utilized and deeply valued ally in humanity’s pursuit of increased power and knowledge.
The Hydraulic System
In a nutshell, a hydraulic system relies on compressed fluid to shift force from one point to another. Picture it like a team effort involving key players: Reservoir, Pump, Valves, Fluid, Motor, Hose, Filter, and Cylinder.
The reservoir is like a holding area for the hydraulic fluid before it gets pressurized. Typically, it’s filled with hydraulic oil which gets filtered to remove any impurities. The pumps then kick into action, pushing the fluid from the reservoir into the system, amping up its energy. And guess who powers the pump? That’s right, it’s the motor’s job.
Inside the hydraulic cylinder, the high-pressure fluid gets to work on the rod and piston. With each stroke, the cylinder transforms fluid pressure into good old mechanical force. As this happens, the reservoir’s oil level takes a dip while the rod and piston stretch out.
But what goes out must come back. When the rod and piston retract, the fluid heads back to the reservoir. The reservoir’s metal walls play a cool role, allowing excess heat to escape. As a bonus, the reduced pressure lets any trapped air bubble out. Remember, if the cylinders have to squish air bubbles, it’s like a hiccup in efficiency.
Now, meet the MVPs: directional control valves and pressure relief valves. Directional control valves steer the fluid’s path, while pressure relief valves act like guardians, preventing pressure overload mishaps. They also keep a check on how much oomph rotary motors and cylinders can put out. These valves swing into action when pressure levels go beyond the limit, letting oil flow back to its cozy reservoir.
The fluid takes a journey from one part to the next in the hydraulic system, all thanks to the trusty hydraulic hose.
Now that you’ve got the lowdown on hydraulics, it’s time to dive into mastering that hydraulic pressure for your safety and your machinery’s well-being.
How to Control Hydraulic Pressure
To achieve hydraulic pressure control the hydraulic systems meter the flow of a fluid. The rule of thumb here is:
Pressure= force to move the load
Flow= how fast the load moves
The actual fluid pressure involved here plays a crucial role in this ‘Multiplication of Force’ and in this context there are two features of hydraulic pressure which is important to remember:
1. Hydraulic pressure is measured as a force per unit of area e.g. Bar (Kg/cm2) or PSI (Pounds per square inch).
2. The Hydraulic pressure at any point within the fluid is the same in all directions provided of course that the fluid is static.
The accepted international standard for maximum working pressure in the high-pressure hydraulic tools industry is 700 Bar (10,000 PSI). The criteria for establishing the maximum hydraulic pressure for a hydraulic cylinder at 700 Bar pressure is the size of the effective area of the cylinder bore.
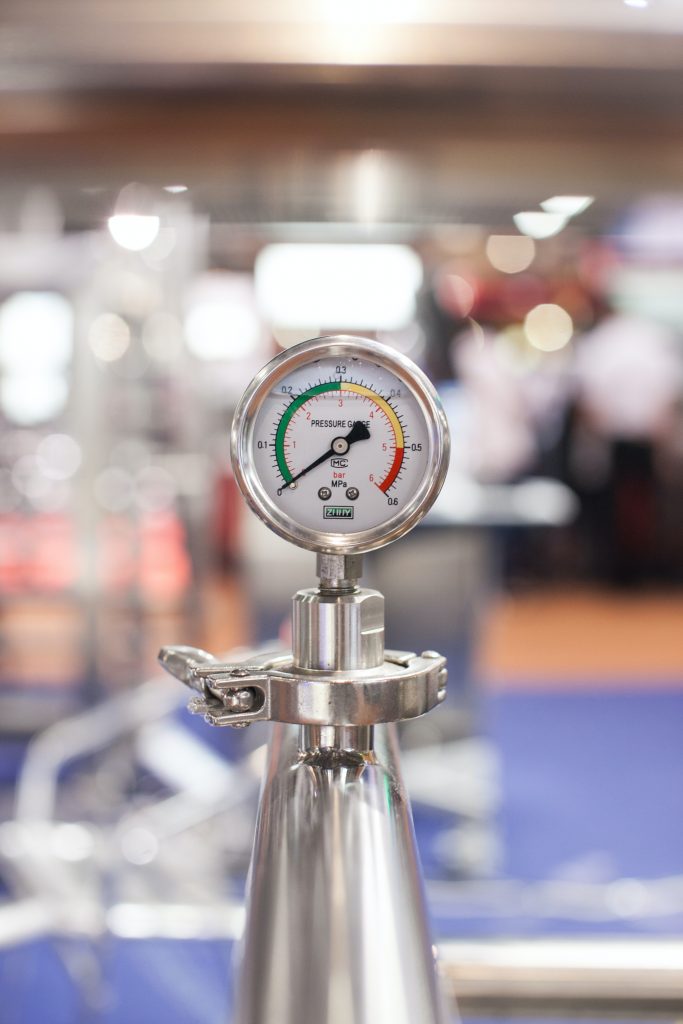
Dangers of Overpressurization
The risks associated with hydraulic overpressurization are not to be taken lightly, as they can pose a significant threat to the stability and functionality of your machinery. This perilous scenario can set off a chain of catastrophic events, ultimately resulting in the breakdown of crucial components in your hydraulic system.
One immediate consequence of overpressurization is the vulnerability of hoses and seals. These vital parts, typically built to withstand specific pressure levels, can buckle under the excessive force placed upon them. This not only jeopardizes the containment of hydraulic fluids but also exposes nearby components to potential harm.
Moreover, the mechanical strength of vital elements like pumps, motors, cylinders, and valves is put at risk. These pieces, precisely calibrated to operate within defined limits, can yield to the overwhelming stress brought on by overpressurization. The result is a distressing chain of failures, hindering the smooth operation of the machinery and causing disruptions in its intended function.
A particularly worrying consequence of overpressurization is valve plate separation. This issue manifests through clear signs like uneasy vibrations and pulsations running through the pressure lines of pumps or motors. As the cylinder barrel experiences separation and re-coupling with the valve plate, the machine’s behavior becomes erratic, mirroring the turmoil within the hydraulic system.
Contrary to a commonly held belief, pushing your hydraulic system’s pressure to its limits does not translate to improved operational speed. This misconception can lead to serious misjudgments, ultimately endangering both your hydraulic system and your personal safety. It’s crucial to abandon this faulty reasoning and instead follow the guidance laid out in the manufacturer’s manual or, even better, seek advice from an experienced professional.
In essence, the perils associated with hydraulic overpressurization cast a long and foreboding shadow over your machinery’s performance and your own safety. Embracing a careful and well-informed approach is the foundation of preventing potential disasters that could otherwise undermine your hydraulic system’s durability and operational effectiveness.
If you have questions regarding any of your hydraulic systems, please contact us today! We’re ready to help any way we can.